Looking after your forklift between services should be a number one priority in your machinery management programme. It’s easy to rest on your laurels after services, but machinery maintenance is more than an occasional job. Between checks, carrying out regular monitoring is important to protect your forklifts for long term use.
We’ve put together our top tips for how best to look after your equipment and minimise the costs associated with damage and wear and tear. It’s worth taking the time at the outside to review the recommendations here and implement an appropropriate regime of checks. Doing so will avoid any nasty surprises when it comes to the service. The last thing you want is to enter your forklift for its service and come back with a hefty bill.
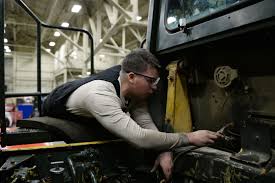
1. Train your people
Make sure your staff (as well as any temps or agency workers) are taking care – forklifts often have lots of users and this can lead to misuse, inconsistencies around equipment management, or gaps in service and care checks. It sounds basic, but taking obvious measures is often the best place to start. Good practice is to have checklists and manuals that are easy to use for all. Simple language and diagrams are the best way to make these accessible. Give your staff regular training in how to care for machinery and ask for their input to make sure you are working to best practices. Those who work regularly on the machinery will know it inside out and be able to identify issues early. If they know what to do and care about keeping things in good condition, you’ll have less to worry about when it comes to your forklifts.
2. Watch those wheels
Check Tyres daily – make sure your forklift tyres have the correct air pressure at all times. Include in your routine maintenance a check for any cuts or flaws in the surface. As well as helping to preserve the condition of your machinery in the long term, this practice can help your organisation day to day. Badly maintained tyres can lead to accidents, damaging your goods and potentially injuring employees too. If your equipment is badly maintained and causes an accident, you could be responsible, so it’s important to avoid that at all costs.
3. Look out for the lights and warnings
Keep an eye on warning functions – making sure the alert gauges and lights on your equipment are working at all times enables you to spot issues before they cause damage to your bottom line (and your warehouse!). The alerts and gauges are designed to enable the forklift to monitor its own maintenance standards. These will be reset at a service. Picking up on problems before they grow or get out of control is likely to mean cheaper repairs, too.
4. Make lists
Run through an easy maintenance checklist – have a maintenance checklist handy to ensure employees are able to do thorough maintenance tests. This builds on point one, the need to train your employees and make sure they are maintaining your equipment in the best possible way. The checklist, which can be used by you or your staff, should include checks for vibration, damage to parts, fluid levels, tyres, overheating, misuse and cracking. Review and build on this regularly.
5. Power up
Check charging and fuel levels – forklifts are available in a variety of power function options, whether fuel that you need to manually top up (gas, diesel, propane etc.) or more convenient electronic battery systems. Maintaining healthy fuel levels/battery charge helps to ensure your machine is working effectively and reduces the likelihood of damage. Make sure you build good fuel management practices into your training and checklists and ensure you have convenient and easy to use fueling ports/systems. There should be no room for excuses when it comes to staying topped up.
6. Keep things moving
Don’t let your machine go thirsty – make sure moving parts are greased and lubricated to prevent running and wearing on components. All necessary fluids should be kept topped up to avoid damage. For example, hydraulic fluids, motor oil and fluids. Change filters regularly and carry out frequent liquid and lubrication checks.
Managing your forklifts between services is a good business practice that pays dividends in the long run. Good practice maintainence leads to lower service costs each year. ultimately, your machines are likely to last longer. Employees will be happier because they will encounter fewer inconveniences and delays caused by errors and poor functioning. Your customers will benefit in the standard of your service and limitations on disruption. Ultimately, maintaining equipment correctly and to a high standard will impact your bottom line. This is not only true of the losses you’ve avoided, but also the gains you’ve made. Saving time and money saves costs and improves productivity. You can do more, for less.